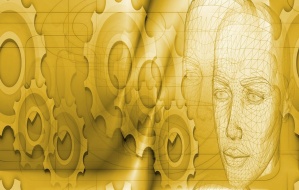
خدمات مشاوره، آموزش و حمایت مالی به استارتاپها
ویژگیهای اصلی انواع استارت آپ برای اینکه بتوانیم یک کسبوکار را در دستهی کسب و کارهای استارتاپی به شمار بیاوریم، مهم است که حضور چند […]
ویژگیهای اصلی انواع استارت آپ برای اینکه بتوانیم یک کسبوکار را در دستهی کسب و کارهای استارتاپی به شمار بیاوریم، مهم است که حضور چند […]
در این مقاله میخواهم چندین مرکز فروش تابلو دکوراتیو در تهران به شما معرفی کنم 1-لابراتوار چاپ عکس نورقائم یکی از مرکز فروش تابلو دکوراتیو […]
معیارهای مهم در انتخاب بهترین گیم سرور چیست؟ اگر بخواهیم بدانیم که بهترین معیارها برای انتخاب سرور گیم چیست، باید موارد متعددی را مدنظر قرار دهیم. درادامه، […]
برای طراحی سیکل بسته لوله گاز مبرد در سیستمهای سرمایشی و طراحی یک سیستم بسته به لولههای مسی نیاز داریم. این لولهها برای عبور […]
مقدمه: همگام با رشد شهرنشینی و توسعه آپارتمانها، نگرانیها درباره امنیت خانهها نیز افزایش یافته است. در روزهای اخیر، دربهای ضد سرقت به عنوان […]
سرویس استیم، که بین گیمرها به خاطر خرید بازیها، انجام استریم، به اشتراکگذاری محتوا و ذخیرهسازی دادهها شهرت دارد، برای برخی کاربران به دلیل تحریمهای […]
شما در گیم فور میتوانید لیست گیم سرور های ایرانی را به راحتی در دسترس داشته باشید، تمام تلاش ما در گیم فور این است […]
خرید آنلاین داروها از داروخانه های اینترنتی در دهه اخیر به شدت رواج یافته است. این روش خرید، به مردم امکان می دهد تا به […]
انتخاب بهترین بیمه تکمیلی: وقتی صحبت از بهترین بیمه تکمیلی به میان میآید، یعنی باید اطلاعات دقیقی در خصوص انواع بیمههای درمان تکمیلی بدست آورد. در اکثر […]
در هواکش صنعتی، تهویه ها از بخش های زیر ساخته شده اند: ورودی هوا: اولین قسمت یک فن صنعتی که برای انتقال هوای بیرون و هوای […]
Copyright © 2024 | WordPress Theme by MH Themes